【Product Overview】
SHMS raw material vertical mill is a grinding equipment that integrates fine crushing, drying, grinding, powder selection, and transportation. It is widely used for grinding various solid materials in industries such as cement, building materials, electricity, metallurgy, chemical, non-metallic minerals, etc. Vertical mills have the advantages of high grinding efficiency, low power consumption, large feed particle size, easy adjustment of product fineness, simple equipment process flow, small footprint, low noise, low dust, simple use and maintenance, low operating costs, and low consumption of wear-resistant materials.
【 Application Fields 】
Grinding and processing of non flammable and explosive materials in the fields of building materials, chemical industry, metallurgy, coatings, papermaking, rubber, medicine, food, etc. with humidity below 6% and Mohs hardness below 7. [Applicable Materials] Non metallic mineral materials with a hardness below Mohs 7, such as steel slag, water slag, graphite, potassium feldspar, coal, kaolin, barite, fluorite, talc, petroleum coke, ash calcium powder, wollastonite, gypsum, limestone, feldspar, phosphate ore, marble, quartz sand, bentonite, graphite, manganese ore, etc.
【 Working Principle 】
The electric motor drives the grinding disc to rotate through the reducer, while hot air enters the grinding chamber from the air inlet. The material falls onto the grinding disc from the discharge port. Due to the centrifugal force, the material moves from the grinding disc to the edge of the grinding disc. When passing through the annular groove on the grinding disc, it is crushed by the grinding roller. The crushed material continues to move towards the edge of the grinding disc until it is carried away by the airflow at the wind ring, while large particles of material fall onto the grinding disc and continue to be crushed. When the material in the airflow passes through the upper separator, the coarse material falls from the cone bucket to the grinding disc under the action of the rotor blades, and the fine powder is ground together with the airflow and collected by the system's dust collector. The collected powder is the ground product. The material is dried in contact with the gas in the shell to achieve the required dry humidity for the product. By adjusting the speed of the separator guide vanes and separator rotor, the fineness of the product can be linearly adjusted.
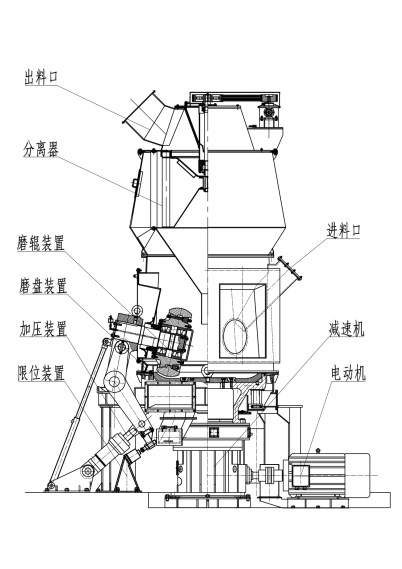
【Main Structure】
The main structure of the grinder consists of a separator, grinding roller device, grinding disc device, pressurization device, reducer, motor, housing, and other parts. The separator is an important component that determines the fineness of the ground powder product. It consists of a variable speed transmission device, rotor, shell, coarse powder hopper, air outlet, etc. It is an energy-saving and fast powder selection device. Grinding roller is the main component for crushing and grinding materials. It is mounted on the bending arm of the grinder, and under the action of external force, it is tightly pressed against the material on the grinding disc. With the drive of the grinding disc, the grinding roller rotates accordingly, thereby crushing and crushing the material. The grinding disc is fixed on the output shaft of the reducer, and the upper part of the grinding disc is a material bed. The grinding disc lining plate has an annular groove, and the material is crushed by the grinding roller in the annular groove. The pressure device is a component that provides grinding pressure for the grinding roller. It consists of a high-pressure oil station, a hydraulic cylinder rod, an accumulator, etc., and can apply sufficient pressure to the grinding roller to crush the material. The reducer is the main component for transmitting power, and the speed of the grinding disc is the speed of the output shaft of the reducer.
【Performance Characteristics】
1) High grinding efficiency and low power consumption;
2) Less metal consumption per unit product;
3) Grinding powder in the material bed with low noise;
4) Negative pressure operation, minimal dust pollution;
5) The process flow is simple, and it can simultaneously complete the functions of material grinding, drying, and powder selection;
6) Small footprint, compact layout, lightweight system equipment, and low investment in civil construction.
【Technical Parameter】